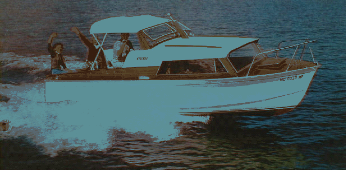
It is November of 1945 and the war is over. The United States Navy decides it no longer wants the molded plywood glider airplanes, being made on the assembly line at Allied Aviation, in Dundalk, MD. The managent and workers stand, looking at the five finished and tested ones they had made and the fifteen more along the way. No further money will be available for operations, now; not even severance pay or rent on the big building. They decide to put the gliders aside and to build boats, using the veeneer, glue and baking oven from the molding operation of the wooden airplanes. Someone told them that the Red Cross needed canoes to teach lifesaving and rescue. Then they were asked to make a fleet of small sailboats for the Naval Acedemy. Soon Allied Aviation was full of boat building activity.( figure one) Each project was a total success, but the allied staff wanted other persuits, so offered the boat operations to the employees, Charley Wingo, Ed Hewitt and Charley Abramo. First these former employees would have to move the equipment out of the rented building. They would have to move everything, at their own expense, to a new – cheaper, workplace. A rented cow barn on the farm belonging to the family that ran Williamson Veneer Company. Once settled, as soon as they could, they began building boats. They built a solid wood hull shape called a mandrel, – on wheels They fashioned a slot for the center keel and stem, to this, were stapled the edge of each layer of veneer. This was made of thin layers of mahogany, which had been coated with heat actuated glue. The layers were put on at a sharp angle to each other so that the grain could give maximum strength in both directions. Outside layers were coated with glue on one side, all the others, – both sides. They were carefully trimmed and fitted together by ladies that were wives and mothers of other employees.After five layers, it was covered with a heavy rubber blanket with vacuum hoses running to a big vacuum pump. The whole affair was then rolled into the autoclave, – a huge oven, and baked at high pressure and steam, for an hour intil, 345 degrees hot! – Really baked! Once out, and cooled and uncovered, the fresh hull was pried off the mandrel, cleaned and sanded. Then it was assembled and finished into a complete boat with transom, rubrails, seats and all features, then finished with varnish, with only the bottom painted a bright color. After a few boats, in 1946, the owner of Allied decided that he wanted to stay in aviation and offered the operation to 3 of his employees, Ed Hewitt, Charley Abramo, and Charley Wingo. All three had appreciated and enjoyed boats and worked closely together with great cooperation on gliders and were also good friends, so it was clear that they would be fully devoted to making a success of the operation.
While building the gliders during the War, they had gotten to know the Williamson Veneer family. Their cooperation and fine quality sawn veneers made an extremily uniform and beautiful product. Most of the veneer they made was for furniture production, so they took a special interest in the quality of the molding veneers, for the now, Molded Products Inc. of Cockeysville, Md.
When the Williamson’s found out that yet another place to work, would have to be found, they offered an unused dairy barn on a farm they owned. Many months of sweat were shed turning that barn into a small boat factory. When Ed and the 2 Charleys found out that the red Cross needed lifesaving canoes, they decided to build canoes. These were dazzling to see, with the beautiful wood and light as a feather, yet ridgid and extremely durable. Then they offered the Air Force a boat to test. They dropped the test boat out of a plane onto land, when it bounced and was still good, they won the contract!
This led to the building of a 35 sailboat fleet for the Naval Academy. Early pictures of the factory have these boats on the floor. As was postwar practice, brothers and sisters, aunts and cousins were employed from the local area. Two of the founders of Molded Products are long term members of the same community, now in retirement.
The three founders, Ed Hewitt, Charley Wingo, and Charles Abramo each provided guidance for the different aspects of boat construction. Ed hewitt was a CPA and office manager and made the advertisements. Charley Wingo did a lot of the design and drawing work, set up the shop and made constant production improvements; Charley was a perfectionist, they said. They all often worked all weekend. Charley was a personable, natural high energy guy that enjoyed smoking as well as racing activities. Everybody smoked cigarettes back then, It gave them an excited, bullet proof, – hard driving attitude. Charley and brother Lou took the boats and motors and raced and set records. They made and offered for sale a cut down model of the winning racer. Following aircraft construction methods, all hulls were minimum thickness and all structural members glued, providing stiffness and ridigity, without extra weight. Charley Wingo and Charles Abramo slaved over the drawing boards together to come up with each new design. Many shapes, sizes and interior layouts were tried to offer something for everyone and to achieve eye pleasing styles. Boats were leak and rattle free while being light, colorful and well finished. In the beginning, attractive aluminim fittings were bought from the Baltimore foundry of H.H. Whiting co. Later brass and then chome plated brass. Charley Abramo was responsible for picking the finest cuts of mahogany planks at the lumberyard in Philadelphia. He was a stickler of high quality and the company put aside their best quality aside for him.The sleek designs and high quality materials made them the lightest, fastest, safest and most beautiful wooden boats ever made. The fully rounded chine asurred that full speed turns could always be made without sliding or loosing control. These features made Whirlwind Boats the lightest, fastest and most beautiful on the water, to this very day.
In 1999, Bob Orgain and Whirlwind World put on a special Whirlwind Commemorative Event at our show with 13 boats on display. Bob gave Ed Hewitt, Charley Abramo and Sally Wingo, Meritorious Achievement Awards during the Whirlwind Lecture. These awards and the Chesapeake Bay Magazine article on Whirlwinds were on display at the funerals of both lifelong friends who died at 92, last spring. The wonderful qualities of the 15,000 boats they produced in the 15 years they built them will remain a lasting tribute to these men and Maryland boat building.
More Wild About Whirlwinds
They were years of hard work, 1946 to 1956. Charley Wingo, Ed Hewitt and Charles Abramo transformed the remains of Allied Aviation into Molded Products, Inc. They moved all the equipment 3 times, put 35 friends and family to work, built pontoon bridges, medical boxes, air rescue boats, canoes that weighed 37 pounds, small sailboats in fleets, for the Navy, larger 24’ sailboats for Luders, in Mass. and Navy lifeboats. They went to the NY boat show every year, signed up 40 dealers, nationwide. They set up shop in rented barns near Williamson Veneer in Cockeysville, MD.
They designed and built several dozen solid wood mandrels on wheels and then molded thousands of boats off of them, baking each until rock solid, in the 30 ft long steel autoclave oven powered by 250 lbs of steam and 150 lbs,vacuum.
They set up and ran a lumber mill, a huge veneer coating department, cutting and shaping departments, assembly rooms and a painting and finishing room.
The three founders worked most weekends improving every aspect of their operation. Designs were constantly critiqued and improved to keep up with the market. Hardware, fastenings, tools, construction methods and advertising steadily evolved over time. Charley Abramo often traveled to Philadelphia, to the Thompson Lumber Co., where he selected the finest, knot free, straight grain mahogany. The record largest board brought by train was 21ft. long 25” wide and 6 inches thick. They were flooded out 3 times and finally bought 3 acres nearby on York Road, the edge of a farm, for $1,000.00 per acre.
They modified their designs and went racing, everyone participated and all had some measure of success. Charley won first, second, and third prizes in a dozen races during the `46 to `49 era. They even sold cut down, stock racing models. Their successes made all the local papers.
They worked all year around, renting local barns and stacking piles of boats for spring and summer sales. The third Charley, – Charles Martin, drove a Chevy heavy duty pickup with a special trailer they built, that could haul 8 boats at a time. He delivered boats throughout the year to dealers all around the United States. Each one was his baby: he kept touch-up paints and varnish on board and made sure every one was perfect before the papers were signed. Once, several boats flew off the top in a huge storm. He took them back to the factory where they were repaired good as new. Since the factory was flooded out 3 different times, all employees were involved in the cleanup operation. It was a great relief to finally move into the new buildings on York Road.
They shipped boats unfinished for do-it-yourselfers, they painted or finished for individual tastes, models were just plain wood or fancy padded and upholstered with blonde decks called avoirdire, – for magazine covers.
A tiny promotional tugboat for kids was made in limited production.
A custom, double ended Cleopatra’s Barge was made for a special customer.
They had a Montgomery Wards contract for Sea King boats, 300 per year were set aside for spring with the special trim. Every year new models and designs were offered to keep the line fresh. Dealers would sell remaining stock as “new”, each succeeding year, a nationally accepted practice. Employees appeared in all ad photos, color was used for the first time when they could afford this luxury.
In 1956 their New York Boat Show visit revealed that changes were sweeping the industry. The narrow, early models needed to be redesigned. For 1957 wider, more family friendly hull widths were introduced. The whole Molded Products Inc. line was changed. Wrap around windshields, solid floorboards, more bow flair and sweeping painted side trim. All bottom colors were now white, hulls used more layers of veneer, fancy new hardware and steering wheels and bigger engine capacity.
In `58 and `59 soft and hard tops were added and model sizes went to 19’ and 21ft. An exciting new cruiser, completely fitted our for weekend outings, was debuted. These were great times.
In 1960 and 1961 sales began to decline, due to the impact of fiberglass boats and the slowing economy. For the second time they built prototype hulls out of fiberglass. The quality of the materials they could buy was not good. None of their craftsmen liked working with the new materials. The methods required were quite opposite of the one they were using. At the New York Boat Show where they had become friends with boat manufacturers all over the country, they found out that some 600 U.S. boat builders had closed their doors. Their larger boats did not sell well. The writing was on the wall. They had done everything they could, but they had to cut the salaries of all employees for 1961. Many cost reductions were made for `62, vinyl decks, pre-manufactured seats, gold flecked steering wheels and different bow treatments but still sales fell.
In December, the final boats were produced, a closeout auction was held, everything left, went to the dump. The buildings and land quickly sold. Ed Hewitt paid every supplier and all the company’s bills. The money from the land and buildings gave the founders a steady income. Fifteen years and fifteen thousand boats were behind them, now. Whirwind boats were the lightest, fastest and most beautiful mahogany boats, – ever made!
Be the first to comment